Comprehensive Pressure Vessel and Utility Inspection Services
Decundi Inspection Services LLC in Houston, Texas, provides utility inspection and pressure vessel inspection services for properly evaluating industrial equipment used in oil or gas companies. We have incomparable technical services that help you assess your equipment's compliance with industry standards for function and safety. Our inspection services cover the following equipment, functions, and components.
Functions Inspected

Components Inspected
Inspection Report
After the actual inspection and vendor surveillance are completed, our inspectors will prepare a detailed report which encompasses all the findings during the fabrication and testing stages. All reports are, in turn, checked by a technical reviewer, who evaluates completeness, before we submit the results to you. It is our policy always to deliver high-quality inspection services and detailed reports.
Compressor Inspection
The inspection of compressor components includes high-pressure hydro testing and assembly of cast cylinders and steel cylinders. The compressor should also undergo a spin test to verify that the parameters listed under the equipment's job specifications are met. The inspector also checks the main bearing, connecting rods, piston rods, crosshead pins, and crankshaft for unusual sounds and temperature levels.
Boiler Inspection
At Decundi Inspection Services, we have several inspectors who are highly skilled in carrying out an inspection of packaged high capacity Watertube Boilers with Burners and Economizer equipped with fans with Dual Drives. A truncated description of the inspections carried out on Watertube Boilers includes (see truncated above) inspection during the fabrication and testing of mud drum, steam drum plus the firebox and convection section where these compartments (the firebox and the convection section) are made from 2″ Ø tubing with wall thickness as specified per scope and membranes with thickness as specified by the job scope. These membranes are welded to the 2″ Ø tubing.
In addition to the above, inspections of Watertube Boilers include witnessing hydro testing, installation of stainless steel anchors over which refractory is installed at specified areas inside the firebox and the outside surface of the mud drum and steam drum at the firebox compartment plus parts of the water wall. After curing of the refractory has been achieved, the surface of the refractory is visually inspected for cracks. As required by the applicable specification for the installation of refractory, all cracks will be subject to repairs as defined by the job scope. In addition, as required by an applicable specification for the installation of refractory, at the completion of curing and drying, hammer testing will be carried out using a 1-pound ball-peen hammer at random locations throughout the installed area of the refractory at the mud drum, steam drum, and water wall. Hammer testing of refractory is carried out for verification that no dull sound indicating voids or hollow spots is heard during these tests.
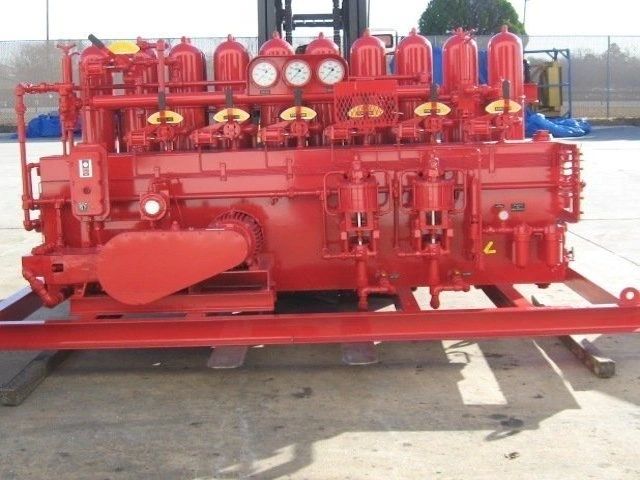
B.O.P Control System
Decundi Inspection Services personnel carried out witness testing during factory acceptance testing of the Blowout Preventer (B.O.P) Control System with sixteen (16) eleven-gallon accumulators (3000 PSI each) with Relief Valve, Fluid Reservoir, and Electric Motor with Triplex Pump Assembly. Additional design parameters include but are not limited to the minimum dry metal temperature of -40° F (MDMT), the maximum ambient temperature of 40º C, PH, HP, RPM, volts, amps, and continuous duty. FAT of this equipment was carried out with satisfactory results.
Visual inspection after FAT found the general overall condition of the Blowout Preventer (B.O.P) Control System includes but is not limited to the pressure/indicating gauges, regulators, oil level glass on the filter housing associated with the fluid reservoir, and stainless steel tubing were all found to be in good condition at the end of testing. Of specific note, the glass lens on the pressure/indicating gauges on the filter housing were found to be free of cracks, not scuffed up, and were found to be transparent (not opaque).
Valve Inspection
Our company employs inspectors knowledgeable about valve inspection. This process includes the set out of valve components prior to assembly, as well as inspection during the hydrostatic tests and function tests of actuated valves.